
But now, faced with increased international demand, manufacturers recognize the benefits of specialized machines able to work most efficiently with their proprietary material formulation and hardness, which can influence the plasticizing and injection system. For example, in the past it may have been sufficient to satisfy demand for different types and sizes of insulators on the same machine. At the same time, the rapidly growing international market for composite insulators has changed the production philosophy of many suppliers. These days, injection-molding machinery has become highly specialized in order to best meet production goals that include handling large volumes with high conformity rate and highest possible productivity.
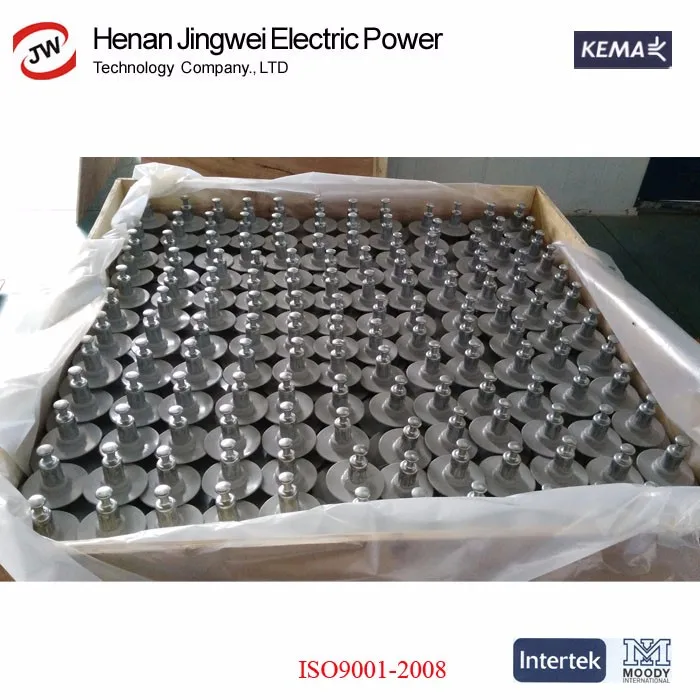
400 kV insulators await second injection-molding operation. In fact, productivity of injection machines for manufacturing composite line insulators has improved continuously since the 1990s when these were mostly adaptations of equipment used to mold products for other applications.

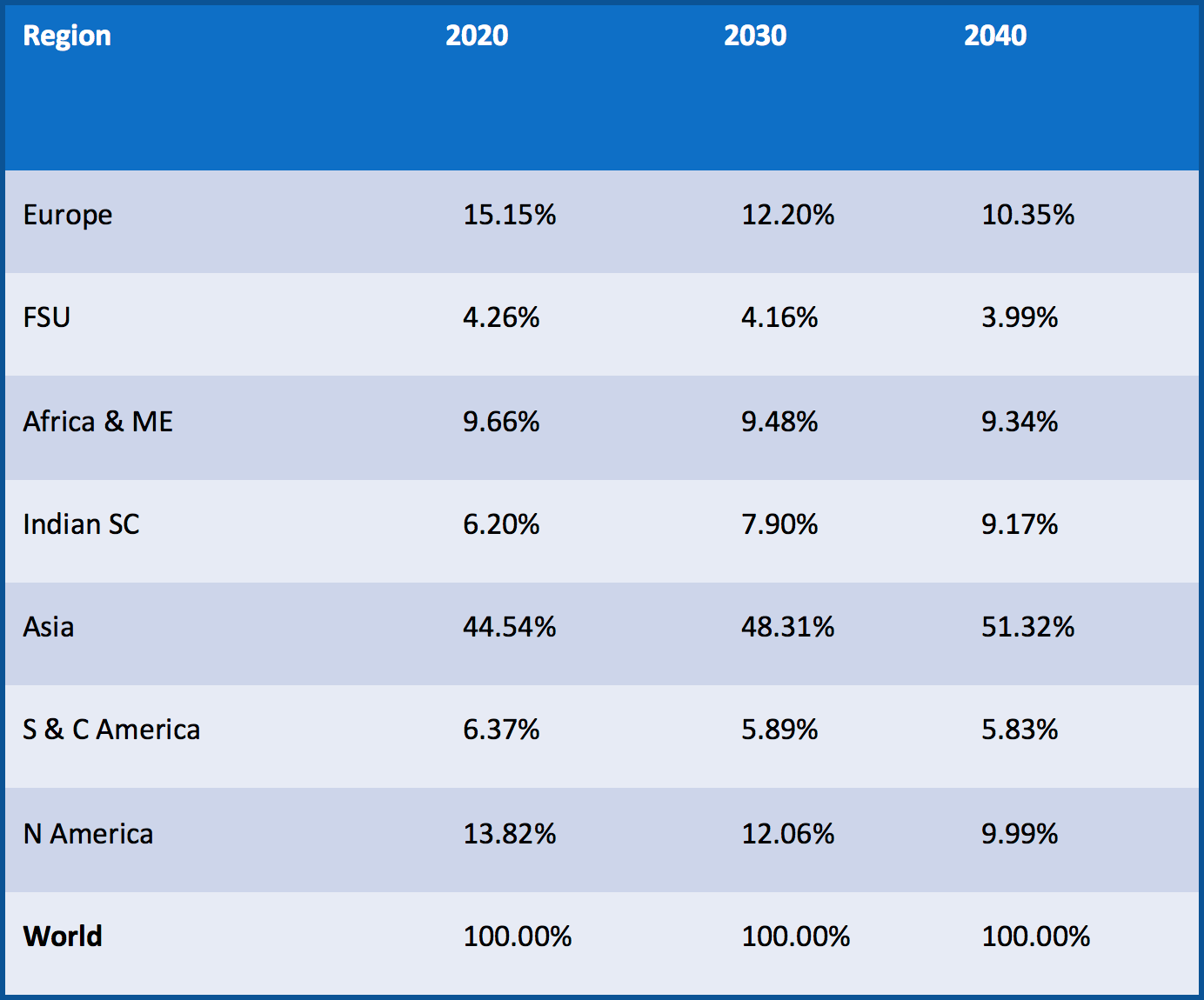
For example, machines have now been designed to mold large quantities of 220 kV line insulators in a single injection shot or alternatively 500 kV insulators in two shots. These are therefore key considerations that influence the purchase of new injection-molding equipment. Precise control is also needed over injection speed as well as temperature and pressure of the injected silicone.Īs order volumes grow, the ability of molding equipment to handle larger and larger production quantities with minimal downtime as well as with high conformity rate becomes critical. Closing by the top mold moving down method helps ensure the rod is kept still before injection. Typical injection-molding cycle for insulators made with HCR silicone.Īnother potential conformity problem is rod displacement, caused if the FRP rod, with or without end fittings already crimped on, shifts from the center of the mold cavity due to excessive machine vibration. From the plasticizing unit, the silicone is transmitted for injection into a cold runner system that ensures the same pressure at each injection nozzle and also optimizes material utilization, thereby reducing wastage. The function of the plasticizing unit for insulators made with a high consistency rubber (HCR) silicone housing is to render the viscous material to a state where it can better flow into the mold, while also removing any air bubbles that might develop during the process. HCR silicone material is viscous and needs to be moved from the stuffer and plasticizing unit into the mold cavity of the injection-molding machine. One factor that can adversely impact conformity during injection-molding, for example, is air becoming trapped in the viscous HCR silicone material as it moves from the stuffer and plasticizing unit into the mold cavity. All determine machine and worker productivity as well as final product quality and cost.Ĭonformity rate is a good measure of the overall level of quality control in a plant. The driving issues for manufacturers of composite insulators include high conformity rate, low wastage of expensive raw materials and shortest possible cycle time. Injection-Molding Technology Injection-molding machines specially designed for manufacturing composite insulators. The sheds are then bonded onto exact locations along the rod to achieve the desired insulator geometry and creepage. The other, referred to as the ‘modular approach’, sees pre-molded sheds slipped over an FRP rod that has already had a layer of silicone material extruded over it. The more common sees the entire housing molded onto the core rod in either a single or in multiple shots on a specialized injection-molding machine.

T here are two alternative technologies when it comes to production of composite long rod insulators applied on overhead lines. The majority of these are located in China, which is also the world’s largest market for composite insulators. This has made entry into this business segment comparatively easy and helps explain why there are now hundreds of suppliers of such insulators worldwide. Unlike for porcelain and glass insulators, scale of operation is much smaller and there is also far less need for intermediate processing and handling. Key factors include the quality of the equipment, molds and sub-components, which include the FRP core rod, the polymeric housing material (whether high consistency rubber or liquid silicone rubber) and the metal end fittings. Manufacturing composite insulators for overhead line applications is mainly a machine driven process.
